- 12-02-2020
- Artículos
Zamak: una aleación con historia
La historia de Gurelan nace junto al Zamak, un material extraordinario que surgió de la unión entre experiencia, tecnología y necesidad. A principios del siglo XX, una creciente industria siderúrgica mundial reclamaba cada vez más materiales baratos, resistentes y fáciles de moldear. Te lo contamos.
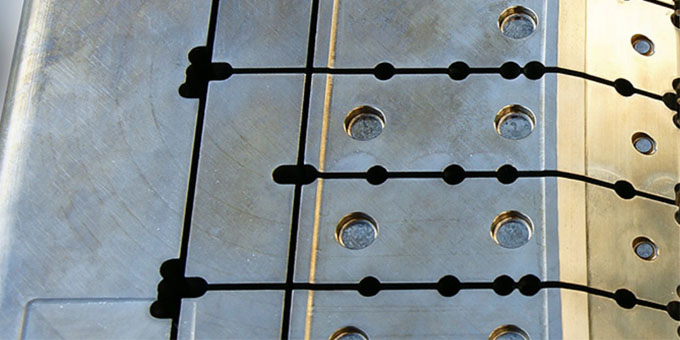
Antes de nada, conviene repasar un poco la Historia. La aleación denominada Zamak surgió entre 1926 y 1929, cuando fue desarrollada y patentada por la New Jersey Zinc Company, una empresa que protagonizó las mayores investigaciones y avances en el mundo del zinc a principios del siglo XX.
En aquella época, la demanda siderúrgica de materiales con determinadas propiedades crecía sin cesar, así como las aplicaciones y subproductos resultantes. Las fundiciones necesitaban un material barato, duro y resistente, fácil de moldear y de mecanizar. El objetivo era obtener piezas de mayor precisión, con mejores acabados y cualidades que la plata, que se ensucia y no se puede pintar.
Inicialmente bautizado como ´Zama´ o ´Mazak´, la New Jersey Zinc Company optó finalmente por el término Zamak, para destacar la importancia del zinc como elemento principal. Esta palabra está compuesta por las iniciales en alemán de los elementos que forman la aleación: Z (Zinc), A (Aluminium), MA (Magnesium) y K (Kupfer, cobre).
Inyección de Zamak en cámara caliente ¿cómo funciona?
La fabricación de productos de Zamak pasa por un proceso industrial específico, condicionado por la aplicación final de la pieza. Por ejemplo, Gurelan fabrica piezas de Zamak para automoción, cerrajería, joyería, electrónica... ¿Cómo se pasa del lingote de Zamak en bruto a una pieza de seguridad para vehículos mecanizada y acabada?
Para empezar, la fundición en cámara caliente se puede utilizar con aleaciones que se derriten a baja temperatura como el zinc, el magnesio... Es posible realizarla tanto en moldes propios, como los que elabora Gurelan de manera exclusiva, como en moldes estándar. La fundición inyectada en cámara caliente es adecuada para metales que no atacan ni erosionan fácilmente equipos como ollas de metal, cilindros y émbolos.
¿Sabes que el Zamak es un material fácil de moldear?
Los lingotes de Zamak se derriten en un horno a unos 420 ºC ubicado junto a las máquinas de moldeado. A continuación, el Zamak fundido se inyecta en las cámaras de la maquinaria de manera muy precisa, permitiendo obtener piezas de diferentes tamaños, pesos y finalidades.
Gracias a su fluidez y a su fusión a baja temperatura, el uso de Zamak permite obtener piezas extremadamente precisas y con formas y perfiles muy complejos. Como empresa familiar fundada en 1934 para la fabricación de artículos de cuchillería (esquiladoras, afeitadoras...), Gurelan fue pionera en incorporar desde su inicio máquinas de cámara caliente para piezas en aleaciones de Zinc (Zamak) destinadas a la elaboración de estas herramientas.
¿Por qué inyección de Zamak y no otros metales?
Tres motivos: calidad, precisión y producción. Resulta muy complicado fabricar este tipo de piezas utilizando otras aleaciones que el Zamak, y mantener al mismo tiempo un control tanto de los costes como de las características industriales del producto. De hecho, realizar operaciones de mecanizado o torneado, pulido y acabado en una pieza de Zamak es más económico y sencillo que, por ejemplo, en una pieza de latón.
Otra gran ventaja: los moldes para la fundición a presión de Zamak tienen una vida útil que en muchos casos puede alcanzar millones de ciclos. Por ejemplo, en Gurelan contamos con moldes que han superado los 4 millones de ciclos en multicavidad. En cambio, un molde para aluminio tiene una duración más limitada, generando un mayor costo que repercute en el precio final de cada pieza inyectada.
Así pues, gracias a su sencilla industrialización, al ciclo rápido y a su baja temperatura de fusión, la fundición a presión de piezas de Zamak genera el punto de encuentro ideal entre costes, precisión, durabilidad y calidad constante, tanto en pequeñas como en grandes producciones.